At its core, CNC milling includes the elimination of product from a workpiece through a series of collaborated motions. When the layout is finished, the operator uses computer-aided manufacturing (CAM) software application to equate the CAD version right into a set of instructions that the CNC device can check out, normally in the kind of G-code.
Among the standout attributes of CNC milling is its versatility. Unlike conventional milling devices, which normally run along 1 or 2 axes, CNC milling machines can operate on multiple axes at the same time-- typically 3, 4, and even five. This capability allows suppliers to attain extra intricate geometries than ever. For example, a three-axis milling equipment can relocate along the X, z, and y axes to create a variety of shapes, while a five-axis machine can tilt and revolve the work surface, enabling access to challenging angles and surfaces. This versatility not only enhances design possibilities yet likewise improves the production procedure, as it lowers the requirement for multiple setups and extensive hand-operated treatments.
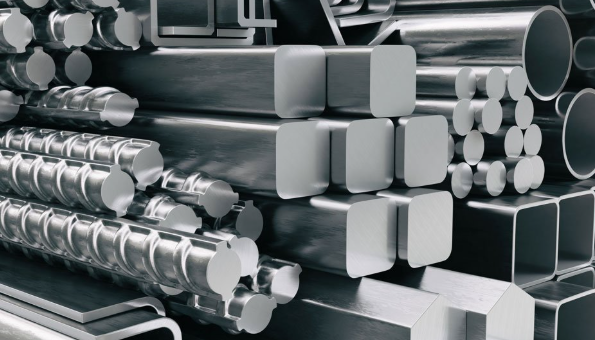
Explore CNC guide the transformative globe of CNC milling, an innovation that integrates precision and automation to generate top notch elements efficiently from numerous products, and discover its procedures, benefits, and essential considerations for success in modern production.
The option of tools is an additional vital aspect of CNC milling. The ideal tool selection can considerably impact the quality of the ended up product and the performance of the machining procedure.
One important aspect to take into consideration in CNC milling is material compatibility. Recognizing the residential or commercial properties of the product, including its solidity, machinability, and thermal conductivity, enables drivers to optimize the milling procedure and attain exceptional outcomes while minimizing wear and tear on devices.
Beyond the technological factors like style, tooling, and products, there are extra factors to consider for optimizing CNC milling procedures. Making use of sophisticated attributes such as toolpath optimization techniques can simplify the milling process additionally, enabling quicker machining cycles and minimizing waste.
Moreover, one of the substantial advantages of CNC milling is the capability to automate recurring jobs, which reduces human error and boosts production uniformity. While traditional milling devices need a skilled operator to manage the manufacturing procedure, CNC milling machines can run unattended, carrying out pre-programmed directions with accuracy. This degree of automation not just improves efficiency however likewise liberates knowledgeable employees from mundane tasks, allowing them to focus on even more useful tasks such as quality assurance and process improvement.
In spite of its benefits, transitioning to CNC milling is not without obstacles. The schedule of leasing options and affordable entry-level CNC milling equipments has made it more obtainable for tiny and mid-sized companies to embrace this modern technology.
Training and ability development for personnel running CNC milling makers are also essential for making the most of the return on financial investment. Operators require a strong understanding of both the CNC maker itself and the software being utilized for programming and tracking. Several producers find success by supplying internal training programs or partnering with outside training organizations to outfit their teams with the necessary abilities and knowledge.
In recent years, technological advancements continue to form the area of CNC milling. As industries progressively transform to automation, incorporating features such as man-made intelligence (AI) and maker learning right into CNC machines can additionally improve the accuracy and efficiency of milling procedures.
Moreover, developments in software are continually narrowing the gap between layout and manufacturing. Modern CAD/CAM systems currently provide extra intuitive user interfaces and boosted simulation abilities, permitting operators to picture machining processes before they are implemented. By spotting possible issues in the style phase, business can settle design problems or optimize cutting approaches without incurring costly changes to physical materials.
In the context of CNC milling, sustainability is likewise gaining significance as suppliers look for methods to minimize their environmental effect. Applying practices such as enhancing reducing parameters, utilizing extra efficient tooling, and reusing products can add to a much more sustainable milling procedure. In addition, technologies such as additive manufacturing are being discovered combined with CNC milling, presenting chances for hybrid production approaches that even more boost sustainability by minimizing waste.
Explore study CNC the transformative globe of CNC milling, a modern technology that combines precision and automation to generate high-quality elements effectively from numerous products, and discover its processes, advantages, and essential considerations for success in contemporary production.
In verdict, CNC milling stands for a necessary possession in modern manufacturing, giving firms with the capability to create complex and high-quality parts successfully. Comprehending CNC milling begins with a strong structure in its processes, including the interplay in between style, tooling, materials, and software. Inevitably, effective assimilation of CNC milling equipment, experienced workforce training, and clever automation leads the way for the future of manufacturing, where quality, performance, and sustainability become the hallmarks of functional excellence.